Produts
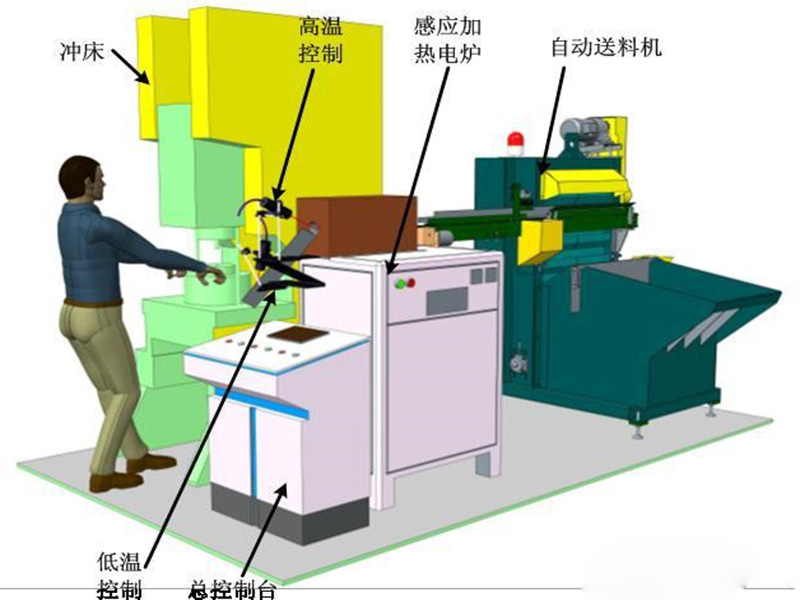


500kw Intermediate Frequency Diathermy Furnace
Equipment power: 500kw
Equipment frequency: 2.5KHz
Heating cycle: 15s/piece
Delivery Time: 3-20 days after confirming order,detail delivery date should be decided according to production season,order quantity and destination.
Warranty: 12 Months
Online Inquiry
-
-
Equipment introduction
500kw Intermediate Frequency Diathermy Furnace
Features of Intermediate Frequency Diathermy Furnace:
The intermediate frequency power supply adopts a fully digital control system, and the core control board is standardized, and all devices can be interchanged, which is convenient for maintenance and debugging. All equipment is equipped with a unified backup control board. When the equipment has a soft fault, only need to replace the backup board. The equipment can be put into normal use in a short time without affecting production. The replaced control board can be repaired in a static state.
Due to the use of digital control, all chips use imported components (Motorola, Siemens, etc.), so the control system has very good stability, and the failure rate is extremely low.
A temperature closed loop interface is designed, and a temperature closed loop instrument can be installed as needed.
100% start-up reliability (regardless of no load or full load).
Automatic Feeding Mechanism:
Automatic feeder (washing board feeder): This machine adopts electric, hydraulic and hybrid drive. The step-by-step loader lifts the workpiece into the chain for feeding and conveying, and the pneumatic propulsion device.
The diameter of the workpiece range is based on customer requirements. The ratio of the length of the workpiece to the diameter should be greater than 1.5 times. See the attachment for the size of the feeder. The maximum weight of the HX-50100 to store the workpiece is about 1000kg. There is a silo shortage alarm device. ,
The man-machine interface adopts two operation modes, buttons or display screens. (There are functions to set feeding time, push plate, push plate down, start, pause, stop, manual feeding, etc.)
The working process is as follows: Pour the workpiece into the storage bin, turn on the switch, and the cylinder will push a row of workpieces upwards. After reaching a certain height, they will roll into the second storage tank. In the same way, they will be pushed up by the cylinder until reaching a certain height. Roll into the chain conveyor belt after reaching the height of the cylinder. After reaching a position, it pushes a workpiece to a fixed position under the action of the isolation cylinder and the horizontal push cylinder, and finally pushes the cylinder into the intermediate frequency furnace.
Feeding Mechanism
This mechanism is composed of a chain conveyor and a cylinder pushing mechanism.
The feeder adopts a motor-driven chain transmission method. The chain adopts large pitch standard specifications, wear-resistant and high-temperature resistant.
The pusher adopts an electromechanical integrated magnetic switch cylinder, and the push stroke adjustment is convenient and accurate. The cylinder thrust has enough margin to ensure the stability of pushing material. Taking into account the unequal multiples of the blank length and the position of the material in the sensor, the cylinder stroke is selected as 600mm. The stroke of the cylinder is adjustable, and the stroke position of the cylinder is controlled by the magnetic switch installed on the cylinder. The pusher adopts an electromechanical integrated magnetic switch cylinder, which makes the adjustment of the pushing stroke convenient and accurate.
Automatic discharging machine (applicable if the length of the workpiece is greater than 1.7 times the diameter)
The automatic discharging machine is composed of frame, motor, reducer, sprocket, chain/sprocket drive, etc. The conveying line speed is about 200mm/sec. When the bar material just runs to the exit of the sensor, the discharging press roller starts to move, and the bar material is quickly taken out of the sensor through the chain driven by the motor.
Temperature Sorting Mechanism
The temperature parameters measured by the infrared thermometer are sent to the general control system, and the general control system judges whether the temperature of the corresponding heating material is qualified, and then according to the judgment results, the blanks are sent to the qualified channel and the unqualified (over temperature, under Temperature) channel.
Temperature Measurement System
The infrared temperature measurement of this set of equipment adopts the TS2 series infrared thermometer, which is domestically packaged by German optris company technology. The infrared thermometer is installed at the outlet of the sensor for temperature detection and temperature display.
Model: TS2M385-1600
PartnersTags:
Induction Heating Shrink Fitting