Produts
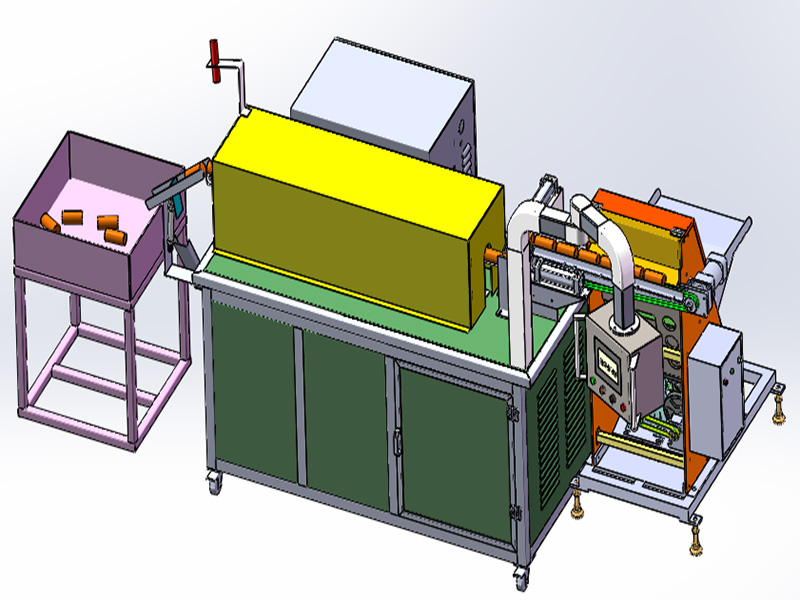


200kw Brass Diathermy Furnace
Workpiece Size: φ46-60, length 60-100
Heating Cycle: 15s/piece
Delivery Time: 3-20 days after confirming order,detail delivery date should be decided according to production season,order quantity and destination.
Warranty: 12 Months
Online Inquiry
-
-
Equipment introduction
200kw Brass Diathermy Furnace
Features of 200kw Brass Diathermy Furnace:
Process Flow:
Process: the feeding mechanism sends the product to the conveyor belt → the conveyor belt rotates to transfer the product to the waiting area → the cylinder pushes the spindle to the feeding area → the cylinder pushes the spindle to the inside of the heating coil → automatic induction heating → the cylinder pushes the unheated product to be heated The product is ejected.
Overall Design:
This system is for induction heating of spindles and bars, equipped with a complete set of automatic heating equipment, including: induction heating part, electrical control and protection part, mechanical part, temperature control part and cooling part.
The induction heating part mainly includes a full-digital induction heating power supply and a diathermic furnace, which inductively heat the spindle to reach a predetermined temperature; the electrical control and protection part uses PLC and touch screen to realize the control and protection of the entire system; the mechanical part It mainly includes workpiece feeding and ejecting mechanism. The temperature control part mainly cooperates with the induction heating power supply to control the temperature of the workpiece to ensure the accuracy and consistency of the temperature control. The cooling part is mainly used to cool the power supply and the induction coil in the diathermy furnace to ensure the normal operation of the equipment.
Process: Before heating, workers set the processing parameters on the touch screen, confirm to save and start processing. Manually place a batch of products on the feeding mechanism, press the start button, the feeding mechanism sends the products to the conveyor belt, the conveyor belt conveys the products to the waiting area, the air cylinder pushes the products to the feeding area, and the air cylinder pushes the products to the feeding area. In the diathermic furnace, the induction heating power supply starts heating, and the infrared probe monitors the temperature of the workpiece. After the temperature reaches the requirement, the next product will be pushed out of the diathermic furnace, and this action is repeated.
Diathermic Furnace Description:
According to process requirements, a variety of bar materials use the same diathermic furnace, so the inner diameter of the diathermic furnace is made according to the maximum outer diameter of the workpiece, and the length is made according to the longest heating length. Insulation effect.
The inductor used in this system is a multi-turn spiral inductor. The coil is wound by a high-quality large cross-section entire rectangular copper tube, and the tube is cooled by water. In order to protect its insulation strength, the coil surface is coated with moisture-proof insulating paint and then solidified into one body. The entire inductor is cylindrical after it is made, and its shock resistance and stability are good.
Screening Mechanism:
The discharge port infrared thermometer detects the temperature of the discharge port spindle. If the temperature of the spindle is too low or too high, the cylinder of the screening mechanism will lift the baffle on the slide, and the unqualified spindle will fall from the gap of the baffle and pass the guide mechanism , Falling into the unqualified product box, waiting for reheating. As shown in the figure, this organization is for reference only.
Temperature Measurement Part:
The temperature control part mainly adopts infrared thermometer and induction heating power supply with digital program to monitor the temperature of the workpiece. When heating the end of the spindle, the infrared probe measures the temperature of a point on the end of the bar, and feedbacks the temperature parameters to the induction heating power supply from time to time. Through the power supply's own digital program, the temperature control accuracy is ensured.
As shown in the figure below, the infrared temperature measurement probe is selected, and the infrared temperature measurement data is transmitted in RS485 digital communication mode, and it is directly connected to the high-frequency heating power supply through the DB9 connector. The connection is simple and the response time is fast.
Partners
Tags:
Induction Heating Shrink Fitting