Technology Exchange
Trends, trends, reviews and prospects
The times are developing and technology is advancing.
New technologies such as 5G, cloud computing, and artificial intelligence are surging.
As a basic process of industrial heating, induction heating is developing rapidly under the impetus of the technological wave and deeply integrated into the technological wave of the times.
The internationally recognized digital, high-cost, all-digital intelligent induction heating power supply has been introduced into the Chinese market by POLARIS-ETeK in 2010 and has been deeply cultivated for more than ten years.
Figure 1 Beichen Yike fully digital control power supply
Introduction of traditional analog induction heating power
supply: Analog devices 3525, 4046, etc. are the control core;
Narrow frequency band: unable to achieve customer's process requirements on a large scale, and even need to manually disassemble and add integrated electrical peripheral components;
Power adjustment depends on manual adjustment of the adjustable resistance knob, based on feeling and experience;
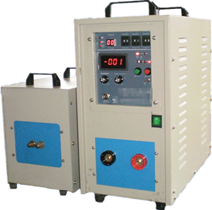
Figure 2 Traditional analog control power supply (Non-Polaris-etek's products)
Due to the harsh working environment and use characteristics of induction heating power supply, high power, high-speed and high-frequency switching devices. The analog system can only provide general protection, and often loses protection due to slow response and execution speed. It cannot be quickly and comprehensively protected, and can only be used for general protection such as water temperature and water pressure. It is often out of protection against short-circuit and fire, which will damage the rectifier bridge or IGBT;
Figure 3 The blown-out IGBT (Non-Polaris-etek's products)
Can not realize the temperature automatic closed loop. It even needs to manually start and stop to adjust the temperature;
The structure is built up and scattered by copper tapes and wires, and cannot achieve electromagnetic compatibility and voltage equalization;
Figure 4 The internal wiring of the analog power supply is messy
(Non-Polaris-etek's products)
Scattered waterways, uneven cooling of multiple nodes, inadequate cooling, frequent water leakage and water blocking;
The process cannot be measured, recorded, and stored, the reproducible production of the product cannot be guaranteed, and the quality is not guaranteed;
It cannot be automatically linked with peripheral equipment and tooling, and needs to be adjusted manually;
Can not communicate with the host computer, can not carry out remote, wireless communication, operation and monitoring.
Polaris-etek's third-generation all-digital induction heating system
POLARIS-ETeK
Keep up with international technology trends,
Perfect combination of digital control technology and induction heating technology,
Committed to the development of intelligent, convenient, efficient, reliable and economical all-digital induction heating system.
After more than ten years of intensive work in the industry, it has been launched to the third generation.
POLARIS-ETeK uses the powerful computing power based on DSP/ARM chips to cooperate with the embedded software system, combined with advanced circuit design as the control feature, to build an intelligent induction heating platform;
Figure 5 DSP/ARM chip
Take the national standard laminated busbar as the main structural feature to achieve electromagnetic compatibility and voltage equalization;
Fully standardized cooling design is the heat dissipation feature;
Figure 6 The third-generation all-digital induction heating system
Induction heating intelligent platform
POLARIS-ETeK The intelligent platform of the all-digital induction heating system takes induction heating power as the main management object, and at the same time intelligently manages the peripheral cooperative equipment of the power supply. It is embedded in the customer's entire management system to realize the customer's product by taking on the process of realizing the customer's process as a means Automated, semi-automated, high-quality, repeatable production.
The core technology highlights of the all-digital intelligent induction heating system
POLARIS-ETeKThe all-digital induction heating system is an IGBT variable frequency power supply based on DSP or ARM control. Automatic resonant frequency tracking (variable frequency adaptive range 1-50Khz), variable frequency adaptive. When the process is adjusted or the load changes, without manual intervention, the power supply can realize automatic frequency tracking and automatically jump to the optimal resonant frequency of the load;
Load automatic matching technology (variable load adaptive). When the load changes, the power of the power supply can be self-adapted for stepless adjustment (adjustment range 10-100%). There is no need to manually adjust the power or control the power through external devices. Our fully automatic intelligent IGBT variable frequency induction power supply has a strong linkage between power, temperature and load. Through the automatic regulation of power, temperature and load, accurate and stable control of heating temperature can be achieved;
High-speed, high-precision temperature closed loop, and can be heated according to the set temperature process curve, the implementation accuracy is 1%;
Figure 8 Infrared temperature measurement forms a temperature control closed loop
Unified management, operation and control of power supply peripheral equipment. For example: hardening machine tools, stepping systems, servo systems, industrial robots, manipulators, etc. From both the hardware and software aspects, ensure the unity between the equipment, realize the systematic linkage and compatibility, and ensure the best matching degree of equipment and process;
Quality monitoring system and quality traceability function. In the form of a database, the events that occurred during operation, including operations, data parameters, faults, alarms, product batches, operator numbers, etc., are fully recorded, and historical data and curves can be quickly searched, and the reasons for quality problems can be analyzed. ways to improve;
Figure 9 Statistics table of equipment operation
Process customization and process parameter control. The all-digital intelligent variable frequency power supply can integrate parameters into the user's manufacturing system and quality control system. The user can modify and compile the processing technology according to the processing technical requirements. The power supply reserves the RS485 interface on the main board, which can be printed or downloaded at any time;
Remote communication operation, monitoring and control. At the moment when mobile Internet terminals are popular. The all-digital intelligent variable frequency power supply system can be directly operated and controlled by mobile phones. DSP/ARM processor collects massive data of operating parameters (such as voltage, current, frequency, power, temperature curve, position, speed), and transmits it to mobile phones, industrial computers, CNC systems, laptops, and PCs via the Internet. Console and remote control room, operate, monitor and control on the corresponding terminal;
Figure 10 Smooth communication
Fast, reliable and comprehensive protection system. The all-digital intelligent variable frequency power supply is based on the powerful computing power of DSP/ARM and embedded software system, which can realize fast, comprehensive and reliable protection of the power supply. In particular, it can be reliably protected against major equipment crises such as short-circuit, ignition, over-current, etc., without exploding IGBTs, or burning rectifier bridges, capacitors and other main components. When the device fails, the screen will display the content of the failure, and you can query the corresponding troubleshooting methods. Quickly judge and deal with it without relying on the technical level and experience of the personnel;
Figure 11 Comprehensive protection and troubleshooting suggestions
Process execution and control. The all-digital intelligent frequency conversion power supply platform is tailored to customers' various process types, such as brazing, quenching, smelting, forging and other personalized process requirements. Another example is the intelligent connection of various process parameters (frequency, temperature, speed, position signal, visual signal, motion signal). You can edit and modify the processing parameters, and store them for recall and printing at any time.
Figure 12 Resource Allocation Center
The above is a brief introduction to Beichen Yike's all-digital induction heating system.
Need to know more, please continue to pay attention.
Solve the pain points of the industry and keep up with the pace of the times.
I hope that the services and products of "Beichen Yike" can contribute to the development of your business.